As part of my general desire to learn how to make and do things myself, I’ve long had an interest in being able to re-purpose metals. Metals, being an incredibly useful and versatile raw material cover a lot of ground when considering things from the perspective of self reliance.
Certainly, by no means am I under any impression that I should do everything myself, nor do I have any desire to, but, it is an interesting drive for knowledge. Today, I finally got around to exploring the process for melting down aluminum for potential re-use. E.G. Recycling.
I’ve been crushing and saving drink cans for a little while now, and had managed to build up a stash of a few dozen cans that I could try out the process on, and while my process was simple and unrefined, it seems to have worked quite well.
There are a number of folks who have done this in “at home” environments, and there are usually two main paths, either using charcoal, or propane as a fuel, and most often improvising some form of forge/furnace. Often made of some form of larger container, with a refractory cement on the inside to form the walls.
I happened to have a barbecue made of a pile of bricks, so I re-arranged the bricks to limit the dimensions, increase the height, and keep more heat in. I separated the pavers forming the base by a small amount to create a channel to provide for air being blown in.
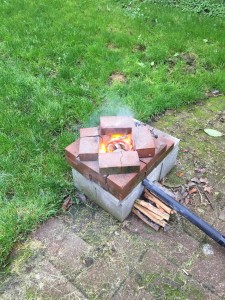
I see a lot of folks improvising a hair dryer as the blower mechanism. I took the hose on my shop vac, and stuck it on the output port. Voila! Blower. This was incredibly effective, though perhaps too effective. The charcoal would burn very quickly, and bring my crucible (a steel pot from Goodwill) to red hot very quickly. I became concerned about over heating the steel and it potentially failing, so I would switch on the blower in “pulses” to moderate the temperature. Something like a graphite crucible would solve this by avoiding concern about the crucible melting.
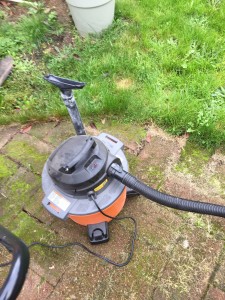
I used the grill portion of the repurposed barbecue as a rack to pre-heat/dry the cans. Despite the cans sitting for a fairly extended period of time, they do retain some liquid. Liquid being introduced to the molten aluminum can cause steam explosions, so I placed the cans on the rack above the coals to bake off any remaining moisture before placing the cans in the crucible to be melted down.
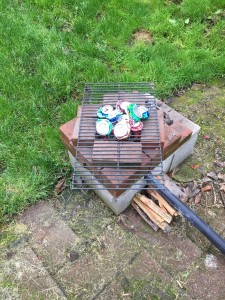
Unfortunately, it’s hard to hold a camera and do anything else at the same time, so I didn’t get any shots of actually pouring the aluminum into my “ingot” mold, which happens to be a heart shaped baking tray I also found at Goodwill.
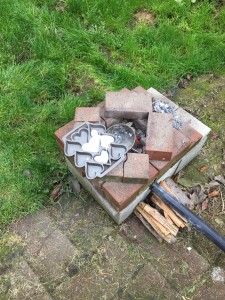
And here’s a closer look of the freshly poured ingots cooling in the mold.
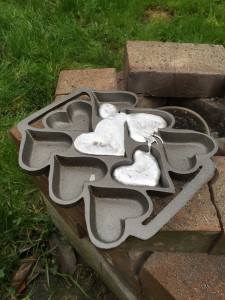
And, a better view from above showing the improvised furnace, mold, and crucible.
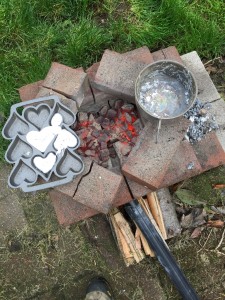
Unfortunately (and to be expected…), the inside of the furnace was far too hot for my infrared thermometer to measure, just giving a reading of “Over High”. Supposedly it’s rated to read up to 608 degrees Fahrenheit.
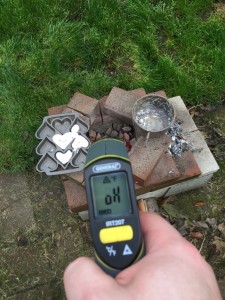
I’ve sprayed some cool water on the ingots to help cool them down more quickly, and flipped them out of the mold for a bit better view.

You can see them continuing to cool on the barbecue grill, as well as my high tech bag of fuel.
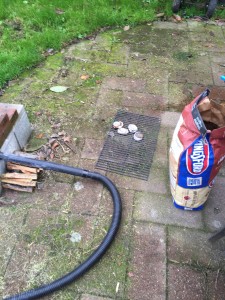
This is the pile of dross I pulled off the aluminum. Unfortunately aluminum drink cans have a lot more than just aluminum in them (paint on the outside, plastic coating on the inside), so there’s a fair bit of waste that comes out that has to be pulled off before pouring. Additionally, it’s clear that there was a fair bit of aluminum that stuck to this dross as I pulled it off, so I will need to experiment with a flux to see if I can get the dross to not pull as much aluminum out with it.
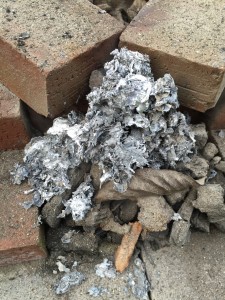
And here’s a closer shot of one of the heart ingots that got poured today.
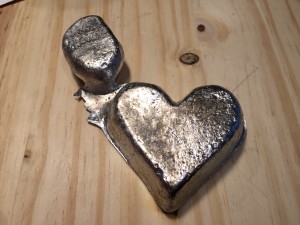
These ingots will eventually be the source of the raw materials for when I move forward to trying to cast things with aluminum. This could potentially be direct parts, but I think my first foray into casting will simply to make rods that I can use as raw stock for work on my metal lathe.